Intelligent Part Alignment at the Push of a Button
hyperMILL® BEST FIT
Are you familiar with this problem? You spend a lot of time, effort, and patience aligning your stock or part on the machine, and, in the end, your finished part does not fit despite all the care you have taken.
We now have a simple, efficient solution for this problem!
Thanks to hyperMILL® BEST FIT, all uncertainties relating to this critical interface are eliminated at the push of a button. You will have no more unpleasant surprises, such as unmachined areas with small allowances, when you open the machine doors after machining. With hyperMILL® BEST FIT, the process is safe, precise, and assured.
“Thanks to hyperMILL® BEST FIT, time-consuming and unsafe component alignment on the machine is a thing of the past. hyperMILL® detects the situation on the machine and aligns the part virtually.”
Manfred Guggemos
Product Manager, OPEN MIND Technologies AG
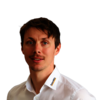
Videos: hyperMILL® BEST FIT
Work smart, not hard
CNC machining? Fun! Part setups and alignment? Not so much…
It doesn’t need to be like that – hyperMILL® BEST FIT is exactly what you need.
Conventional Part Alignment – a lot of effort but little safety
Up to now, it has been standard practice to adapt the part and the clamping in the machine to the conditions of the NC program. The part is aligned manually, using a dial gauge, controller cycles, plus a great deal of care. The real world (clamping) is adapted to the virtual world (programming). This is a time-consuming process that often is repeated several times, and yet the result is often uncertain in the end. This is a real problem for everyone involved, whether machine operators, department heads, or management.
Real-time Alignment with hyperMILL® BEST FIT – fast, safe, precise
With hyperMILL® BEST FIT, we have developed an intelligent part alignment procedure that is integrated in the CAM system, and therefore offers an efficient solution to this problem. The idea: real-time alignment in CAM. The unaligned part is probed on the machine using 3D probing, and the probing points are sent back to the CAM system in the form of a probing report. hyperMILL® BEST FIT then adjusts the NC code exactly to the real part position. So the virtual world (programming) is adapted to the real world (clamping), and not the other way around! The adapted NC code is then simulated in the virtual machine on the actual clamping setup, and automatically optimized using the NC Optimizer. To ensure a safe and accurate process, the machine operator then performs a verification probing. After that, the machine operator can start machining without having to align the component on the machine manually. The advantages include immense time savings, safe machining, and assured processes!
Would you like to learn more about hyperMILL® BEST FIT?
If so, please contact OPEN MIND Technologies.
Advantages
- Safe machining
- Complex clamping/measuring equipment is not required
- Assured setup times and processes
- Shorter throughput times
- Clamping/Alignment skills are not required
- Reduced design effort → Auxiliary geometry is not required
- Zero-point adaptation on controller is not necessary
- Easy to adapt the programming to a different machine
Features
- Fast and reliable part alignment in the CAM system in real-time
- Simulation of the actual part position in the virtual machine
- NC output on the actual part position
- Automatic compensation of machine limits and collisions