Commitment to quality
and productivity
Aerotech Peissenberg GmbH & Co. KG | Peissenberg (Bavaria), Germany
Aerotech Peissenberg relies on CAD and CAM systems from OPEN MIND
The aviation industry sets very high standards for its suppliers. This is especially true for companies that supply rotationally symmetrical and prismatic components that are used in modern engines. The conditions and requirements for such companies are therefore very strict. All employees at Aerotech Peissenberg GmbH – founded around 20 years ago out of the MTU Group – are aware of the high demands that are placed on them. Qualified employees and modern technology are essential for making this possible. The aviation company has managed to reduce processing times for various components by around 30 per cent thanks to the innovative roughing strategies provided by the hyperMILL® MAXX Machining performance package from OPEN MIND, among other things.
“As beta testers, we are always very involved with the new developments in hyperMILL®. We also know how swiftly the company works and how qualified its employees are. We feel like we are in good hands.”
Hermann Stork, Head of NC Programming at ATP
The innovative company’s core competencies include the complex mechanical machining, surface finishing and checking of diverse safety-critical components made of alloys that are difficult to machine and have diameters of up to 1250 mm. Almost all modern multi-stage engines use these components, says Tolga Bayraktar, Head of Technology at Aerotech Peissenberg. The aviation engineer continues: “I always feel safe when I am sitting in an airplane as a passenger, since the safety-related components in almost all passenger aircrafts in the world are built by us.”
But the experts at ATP are not only sought after for their extensive expertise regarding production. Their knowledge is also crucial for new components while they are still in the development stage, as Tolga Bayraktar explains: “Of course, our customers come up with design ideas for the engine components. However, our employees’ expertise is vital when the time comes to select a design that is suitable for production.” What matters in the end is not simply the functionality of the blisks, impellers, spools, rings, housing, and so on. What is equally as important is manufacturing the components in a timely manner at reasonable costs – through what is also known as the Design-to-Cost process. Aerotech designers have a wealth of knowledge about optimal production technologies and processes and can make exactly this process achievable.
ATP offers a wide range of technologies
Once the development stage comes to an end, the component’s design has been agreed on and the order has been placed, ATP implements the production process. The company orders the raw materials that are required and determines how the entire production process should be divided into internal and external supply chains. The wide range of technologies available to ATP is helpful here. It includes CNC turning and milling, combined machining technologies, broaching, balancing, plasma jets, etching, cleaning, as well as labelling, high-precision measuring and the ability to detect cracks.
The engine supplier regularly invests in new machine technologies in order to guarantee a highly efficient production process. These are primarily used for manufacturing new products or when there is a demand for achieving significant gains in productivity. The reason for this is that once the customer gives their approval, the whole production process as well as the machines and tools to be used are ‘frozen’. Making any improvements would require another costly inspection and approval procedure, which in turn would take a long time and cost a lot of money. The inspection and approval procedures are a matter of course in the eyes of experienced aviation expert Bayraktar: “There is no other industry where the safety of the components is as important as it is for aviation, so it is perfectly clear that our customers require a process that is 100 per cent transparent and why we as a company guarantee this.”
ATP has maintained a positive sales trend for many years, which indicates a high level of customer satisfaction. The company consistently receives positive feedback from its customers, especially regarding expertise, quality and reliability. Tolga Bayraktar says that the one disadvantage Aerotech Peissenberg has is the higher costs it needs to pay as a result of the company location. “The wages are significantly higher here than they are in the Far East. But the creative ideas that our employees and partner companies come up with and the expertise that they have more than make up for this and allow us to stay competitive.”
Optimised CAM programming increases manufacturing productivity
The Head of Technology cites the many improvements made to the CAM programming as an example. These improvements were the result of the successful collaboration between ATP programmers and the experts at OPEN MIND Technologies AG, Wessling, Germany. The company first began to use hyperCAD® and hyperMILL® around ten years ago and has expanded its use of the solutions since then. It now uses the solutions for virtually all programming work for milling machines and will also gradually use them to carry out mill-turning and turning processes. What seems to be especially helpful is the compatibility between hyperMILL® and the software used for managing tools and planning company procedures.
Hermann Stork, Head of NC Programming at ATP, is also pleased with the high potential for innovation at OPEN MIND: “As beta testers, we are always very involved with the new developments in hyperMILL®. We also know how swiftly the company works and how qualified its employees are. We feel like we are in good hands.”
Aerotech Peissenberg conducted several comparison tests to find out whether the most recent optimisation solutions achieve anything in practice. For example, the company programmed its roughing process for housing parts made of high-alloy steel both with and without the high-performance cutting module in the hyperMILL® MAXX Machining performance package. The results showed that the processing time could be reduced by around 30 per cent. The improved milling strategies have also improved production times when working with cones made of powder metal.
The secret behind the roughing module in hyperMILL® MAXX Machining is that it intelligently separates spiral and trochoidal toolpaths and dynamically adjusts the feedrate to suit the prevailing cutting conditions. This allows the user to achieve a maximum stock removal rate. Andreas Leser, Sales Director for Germany at OPEN MIND, tells us that the powerful HPC roughing module can be used for all types of machining, whether it is for 2D, 3D or 5‑axis operations. He continues to say: “Our customers also benefit from our role as a pioneer of 5‑axis technology, because they can also use hyperMILL® in a unique way for the 5‑axis machining of curved parts.”
ATP programmer Hermann Stork has increased productivity in a similar way when working with engine discs, where a small tool is used to deburr the edges of what are called the ‘loading slots’. This manufacturing process, called the Mechanical Edge Process (MEP), is very precise and could only be carried out thanks to hyperMILL®’s 5‑axis machining.
New functions for hyperCAD®-S and hyperMILL®
OPEN MIND and ATP also discuss new additional functions for hyperCAD®-S and hyperMILL® together as a part of their close, collaborative partnership, which in turn also leads to modifications to the functions. These functions include new turning functions and a function that optimally limits the feedrate during milling. According to Hermann Stork, milling with angle heads will also become uncomplicated and straightforward in the future.
Hermann Stork is very pleased with how easy it is to operate hyperCAD®-S. He also adds: “There is an incredible amount of potential in the current version of the software. I am extremely well prepared for virtually all eventualities after just one week of CAD training, one week of milling training and three days of training for turning processes.”
Gallery
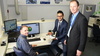
From left to right: Hermann Stork, NC programmer and Tolga Bayraktar, Head of Technology at ATP, together with Andreas Leser, OPEN MIND’s Sales Director for Germany, are pleased with their successful collaboration and the fact that the roughing module in hyperMILL® MAXX Machining can reduce the production times for several ATP components by more than a third.
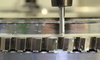
…This is then translated by the postprocessor and transferred to the machine via the networks. The NC experts at Aerotech Peissenberg optimise the component programs during several iterative loops until the customer makes the final inspection. No changes may be made to any part of the production process once the final approval has been given.