CAM software for Modelling and Prototyping
From idea to reality
The goal in modelling and prototyping is to convert ideas into physical models and prototypes as quickly as possible. At low unit volumes, the CAM software must ensure low-cost programming and production.
The look, feel, and function can be optimally tested on a first physical component. Technical prototypes play the central role when it comes to assessing the suitability for use in production.
CAD for CAM – prototyping can be that easy
hyperCAD®-S features an integrated interface package for importing, analyzing, and processing both simple and complex models or prototypes with ease. The CAD software from OPEN MIND also takes existing product manufacturing information into account. hyperCAD®-S offers intuitive filter and selection functions for convenient and fast NC programming.
Direct modelling in hyperCAD®-S makes it easy to make changes to the component and thus create multiple variants. The shape and position of selected surfaces or features can be easily changed. Direct modelling also works with imported external data.
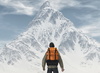
Industry Challenges
-
Reduce setup times
Thanks to complete and multi-axis machining using mill-turn and 5‑axis technologies
-
Shorten machining times
With innovative HSC and HPC strategies for roughing and finishing
-
Increase process reliability
Through collision-tested toolpaths and state-of-the-art simulation technology
-
Improve quality
Blending cycles minimize additional finishing processes
-
Batch size 1
Requires high process reliability
Videos: CAM software for Models Prototypes
North Bucks Machining Ltd
Stewart Palmer talks about their CNC machined downhill bike and success with CAM software hyperMILL®.
Optimal milling results from 2.5D to 5‑axis
hyperMILL® CAM software allows the user to quickly achieve the best milling results. Numerous efficient milling strategies make it possible to produce top-quality prototypes and master forms with the optimal surface finish; time-consuming post-processing is no longer necessary.
5-axis simultaneous strategies are just as easy to program as 3D strategies. The use of short, stable tools associated with these strategies lead to maximum process reliability in the production of complex workpiece geometries. Innovative blending cycles for finishing and rest material machining help to avoid visible transitions and edges. The result: flawless surfaces.
Would you like to learn more about our complete CAM solution for Models and Prototype Machining?
If so, please contact OPEN MIND Technologies USA, Inc.
1492 Highland Avenue, Unit 3, Needham MA 02492
Request an Online Demo.
CAM Strategies for Industry-specific Components
3D strategies
hyperMILL® MAXX Machining
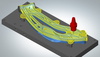
Finishing
hyperMILL® finishing strategies are easy to program and guarantee top-quality surfaces. Whether it comes to 3D or 5-axis machining, hyperMILL® offers the matching finishing strategy for every application.Performance Package: HPC roughing
Are you looking to quickly create a model or prototype from an unmachined part? That’s easy with the high-performance milling strategies from hyperMILL®. Trochoidal toolpaths guarantee reliable, tool-friendly machining with high stock removal rates, regardless of whether 2.5D, 3D, or 5-axis machining is required.
Reliable simulations ensure reliable processing
hyperMILL® offers a reliable simulation feature, including collision control and avoidance, to ensure consistent and dependable modelling and prototyping. hyperMILL® VIRTUAL Machining features an NC codebased simulation that incorporates the geometries and kinematics of all possible components of the manufacturing process. Users are shown the exact machine movements during the simulation that will be performed later on the machine tool.
Advantages at a Glance
- CAD for CAM: hyperCAD®-S for optimal component analysis and processing
- Optimized roughing and finishing strategies: for highly efficient, tool- and machine-friendly machining
- Best-in-class 5-axis strategies: for the reliable machining of complex geometries
- Integrated solution for all machining operations: milling and turning in a single user interface
- High process reliability: perfect milling paths as well as reliable simulation and collision avoidance
- Easy to program: intuitive and supported by automated functions