Probing on the CNC machine for more productivity
hyperMILL® PROBING
hyperMILL® PROBING is the optimal CAM solution for programming measuring and probing operations directly on the machine tool. This will decrease throughput times and at the same time ensure the quality of components.
A well-functioning interface between the CAM programmer and the machine operator is essential for a reliable production process. However, there are a number of issues that need to be dealt with here, such as clamping errors, stock inaccuracies, or operator errors on the machine. Manual interventions and the associated machine downtimes are often hidden time sinks that increase throughput times. Thanks to hyperMILL® PROBING’s process-integrated measurements, these hurdles can be overcome efficiently.
Videos about Probing cycles
On a HEIDENHAIN control
hyperMILL® probing cycles on a HEIDENHAIN control.
Benefits of probing strategies
- Process-integrated measurements improve efficiency
- Shorter throughput times
- Accelerated quality assurance process
- Less scrap
- Increased reliability
Before CNC milling – Set up workpiece
OPEN MIND has designed its measurement solution for the entire machining process. This begins with setting up the workpiece if touch probe systems set the origin or ensure that the workpiece is perfectly aligned.
Check stocks
It is often necessary to check the stock dimensions before machining due to deviations in the saw cut or casting and welding inaccuracies.
Check clamping
The position of the clamping jaw can be checked via probing to verify the clamping.
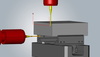
Set up workpiece
Origin definition (rotation): Stocks can be easily probed to align them precisely with the machine axis. This ensures optimal clamping and reduces the amount of scrap.
Origin definition (position): The component origin can be defined quickly and reliably and loaded into the machine control.
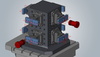
During CNC milling – Measure and adjust
The workpiece is optimally clamped and the stock dimensions are verified. Internal process measuring during NC machining in particular makes it possible to detect and respond to manufacturing errors early on, for example, if deviations in dimensional accuracy are identified after roughing or semi-finishing.
Active process control
Inaccurately measuring of the tool or tool wear often cause errors and deviations. Thanks to hyperMILL® PROBING’s active process control, these errors can be eliminated. Here, a measurement is simply carried out after roughing or semi-finishing and the measurement result is transferred to the control. If deviations occur, they are automatically compensated during subsequent machining. The program run can also be stopped if the tolerance is violated.
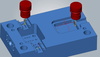
After CNC milling – Quality control
Before the component is taken off the machine, the component inspection is carried out in the original setup. The finished, machined workpiece is compared with the CAD geometry in a target/actual comparison. Thanks to touch probe support, many features can already be reliably measured on the machine tool. This first good estimate of the quality can prevent problems that occur later on a coordinate measuring machine. It also prevents to reset the part on the machine if a correction is needed. This results in shorter throughput times, while quality is guaranteed to remain consistent.
Measure component
Performing quality assurance directly on the machine tool offers numerous advantages. The measurement results are automatically provided in the control system. This significantly increases the efficiency within the process and, in turn, reduces the throughput times. The measurement logs can then be output.

3D point probing
One of the highlights is 3D point probing with which even free-form surfaces can be probed. The probing can be carried out indexed on 5‑axis machines.

Would you like to find out more about the topic of probing?
Do you want know which controllers are supported by OPEN MIND’s postprocessor technology?
For contact:
OPEN MIND Technologies USA, Inc.
1492 Highland Avenue, Unit 3, Needham MA 02492
Features of hyperMILL® PROBING
- All the probing strategies are fully integrated into the NC code, which is translated into the language of the probe control.
- With all strategies, the probe is as easy to program as a standard tool
- Support for 3‑axis and 5‑axis machines for indexed probing
- All the movements of the touch probe are checked for collisions
- Informative process control: It is possible to generate measuring data easily for the individual component geometries and access it from the controller.
Strategies for probing*
- Workpiece alignment along holes
- Workpiece alignment along edge
- Rectangular probing
- Circular probing
- Slot/Rib probing
- Axis-dependent probing
- 3D point probing
*Scope of delivery depends on the control type.